企業ICT導入事例
-旭鉄工株式会社-生産性向上、CO2削減まで成功した製造会社のDX戦略
記事ID:D20029
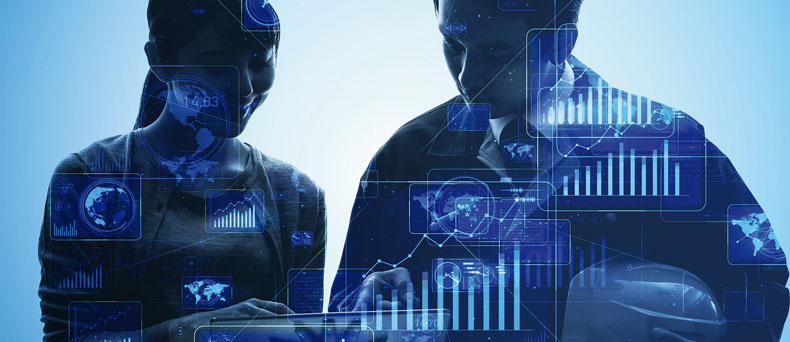
旭鉄工株式会社は、創業より80年以上の歴史を持つ自動車部品の製造会社です。同社は近年、ICT/IoTを活用したDXに積極的に取り組み、生産性向上や効率化を達成、大幅な収益改善を実現しました。自らDX戦略の先頭に立って現場をリードする代表取締役社長の木村 哲也氏に、同社の取り組みのポイントや、DXの推進に必要な考え方をうかがいました。
老舗が陥っていた高コスト体質からの改善
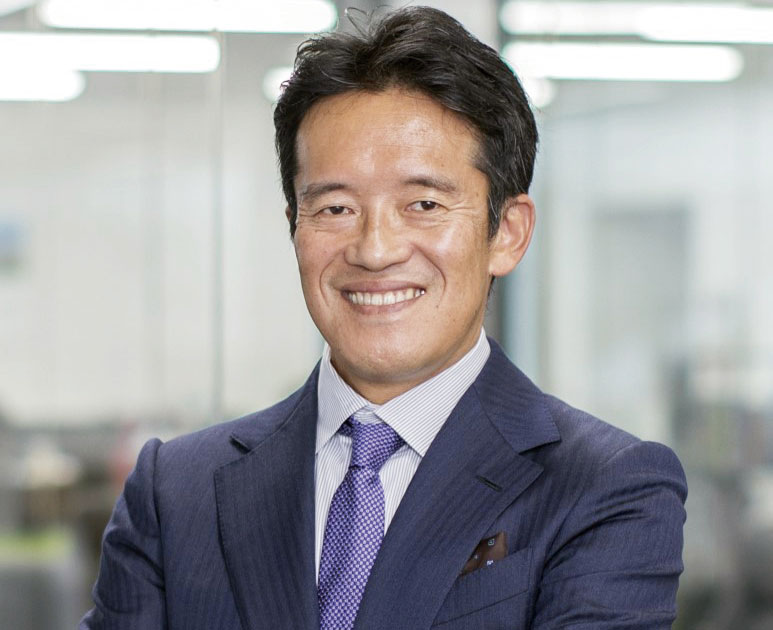
代表取締役社長 木村 哲也氏
旭鉄工株式会社はトヨタ自動車の一次サプライヤーで、長年主要取引先の要望に応えてエンジンやトランスミッション、サスペンション部品などの製造に携わってきました。一見順調な経営状態が予想されますが、2013年に同社に入社した木村氏は、会社の実態を知るにつけ、その将来に危機感を抱いたと言います。
「私が入社した頃の旭鉄工は、収益性が低く、適正な利益が得られない高コスト体質の会社でした。経営陣の将来に対する展望は希薄で、従業員は新しいチャレンジに消極的でした。主要取引先との安定したビジネスに固執する従来通りの経営が、いつの間にか赤字体質と、変化や改革が苦手な企業風土を育てていたのです。将来、人口減少による国内市場の縮小が確実な中、このままでは利益が出せなくなるのは明白でした」(木村氏)
この状況を変革するために木村氏が挑戦したのが、D X でした。ICT/IoTを起点とした大胆なDXによる生産性と収益性の向上です。また、会議時間の短縮、配布資料の廃止、人事異動の活性化、実力主義の昇進、リモート会議の推進など、これまでの組織文化や仕事のやり方の改善に努めました。そして「カイゼンの進まない会社には3匹のサルがいる」と考える木村氏は「見ザル」(問題が見えていない)、「言わザル」(情報やノウハウが共有されていない)、経営でICT/IoTを活用できていない「使わザル」の「3ザル退治」を徹底して推進しました。
ICT/IoTを起点とするDXで「3ザル」を退治
「『見ザル退治』は、ICT/IoTで数値を“見える化”するだけでなく、その数値(問題)に基づいたアクションが重要になります。例えば多くの製造ラインは頻繁に停止し、サイクルタイム※の延長が生じていますが、多くは見えていないので、問題視されることはありません。停止時間の大きな『ドカ停』と比べて、『チョコ停』は軽視されがちなのです。しかし、製造ラインを0.01秒単位で計測している弊社のICT/IoTではサイクルタイムの遅れやチョコ停が、いかに大きな損失につながっているかが“見える化”されています(図1参照)。そうすると損失を減らそう、と自然になるわけです。例えば、チョコ停の削減に取り組んだ結果、1日に1,000個の生産が必要なラインで、これまで1時間に100個だった生産数を125個に伸ばすことができたとしましょう。わずか25個の増産に過ぎないように見えますが、従来は10時間かかっていた作業時間が8時間で可能になり、1日2時間の残業時間の短縮に結びつき、年間200万円以上の労務費の削減になります。弊社はこういうカイゼンを全社的に徹底し、年間4億円の削減を達成しました」(木村氏)
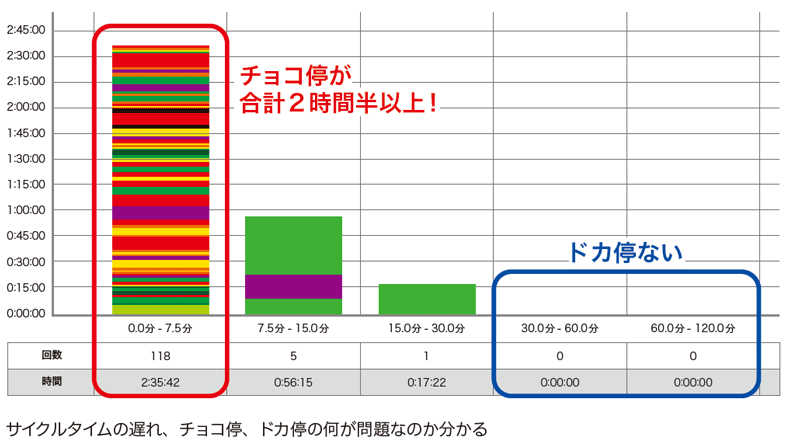
図1:サイクルタイムにおける「チョコ停」の寄与度
「言わザル」の解消には、社内で情報を共有しやすい環境が必要でした。そこで、同社は組織内での情報共有の促進や伝達の仕組みを整え、全社で情報をリアルタイムで共有できる社内SNSの仕組みを構築しました。これにより、現場の社長報告会の内容も10分後には社内SNSに内容がアップされるなど、リアルタイムでの情報やノウハウの社内共有を実現しています。
「このような仕組みを構築し、経営者自身が率先してDXを経営に活用することで、『使わザル』の退治にも成功しました。やはり経営者自身が変革し、率先してDXを推進することが成功への近道だと思います」(木村氏)
こうして推進された同社のICT/IoTを起点としたさまざまなDXは、今では年間10億円、累計で約40億円の利益効果を同社にもたらしています。また、2015年には162億円だった損益分岐点が、2022年には133億円まで下がり、同じ売上でも10億円の収益改善を達成しました。
全社で改善成功例を共有しDXに前向きな風土を創出
3ザル退治を起点とした同社のDXは、カーボンニュートラルの取り組みにも活用され、ICT/IoTを活用した消費電力量の削減でCO2排出量を減らしながら利益を生む、「儲かるカーボンニュートラル」を実現しています。
「電力使用量を単純に数値化しても、それだけではどこに問題点があるか分かりません。そこで、弊社は正味電力(現在使用している電力)、停止電力(設備がトラブルなどで停まっているが通電はしている)、待機電力(夜中など、稼働していないのに通電している)の3パターンで“見える化”しました(図2参照)。これにより、停止電力や待機電力などの無駄な電力が一目瞭然となり、待機電力の電源をカットするなどの改善を行った結果、電気使用量26%の削減と、年間で約1.5億円のコストダウンを実現できました」(木村氏)
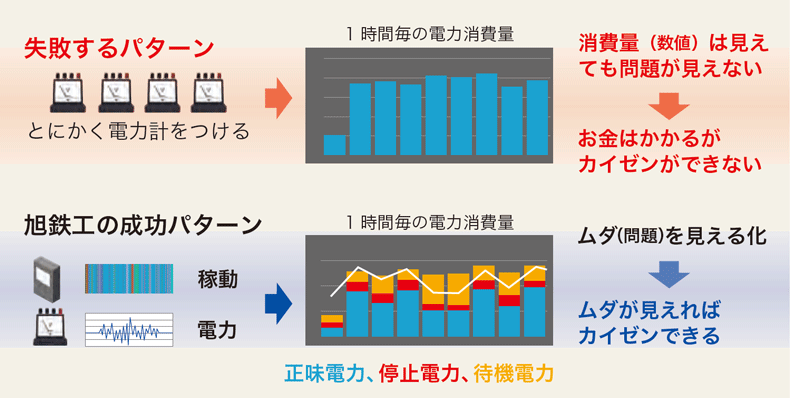
図2:“見える化”すべきは数値ではなく問題
さらに現在、同社では「ChatGPT」を活用した、より効率的なDXの実践にも取り組んでいます。これまでに蓄積された改善例を「Chat GPT」に読み込ませ、「電力削減の事例を教えて」「切削加工機の製造時間を短縮したい」などの質問に対して必要なノウハウを抽出し、回答してくれる「カイゼンG A I」を開発しました。これにより、同社が所有する膨大な量の事例データから、必要な情報を迅速に取得することができます。
「また、ICT/IoTで収集したデータから問題点を教えてくれる『AI製造部長』も稼働中で、毎朝決まった時刻に前日のデータ状況をラインごとに報告してくれています。例えば、『S-01ラインの〇月〇日の稼働時間は目標が15.5時間で、実績が12.1時間』『出来高率が目標の96%に対し実績は85%』といった内容のもので、これまで人間が行っていたライン状況の確認時間が大幅に削減されました」(木村氏)
このようなDX推進における重要ポイントとして、木村氏は「DXに挑戦する風土づくり」を挙げます。例えば、同社は“見える化”された問題に対する改善結果を報告する「カイゼン卒業式」が3ヵ月ごとに行われ、その報告会に木村氏は必ず出席し、労をねぎらい、成果を社内SNSで全社に報告しています。このような取り組みで、社員のモチベーションと改善マインドを上げています。
「DXで得られたノウハウや情報を現場と共有する意識が大切です。自分たちの努力の効果が数字で確認できることで、仕事がおもしろくなりモチベーションが上昇します。DXの成果が数字で可視化されると、現場の改善マインドが上がります。いつの間にか現場に自主的に次のDXに取り組む風土が生まれ、おのずと改善された事例は増加し、会社のさらなる効率化へとつながるのです」(木村氏)
経営者が率先してDXに取り組み、現場のモチベーションを尊重して実現した同社の成功事例は、現在ICT/IoTの導入を検討している企業にとって、有益なヒントがあると思われます。
- ※ サイクルタイム
- 一つの製品の工程開始から完了までにかかる時間のこと
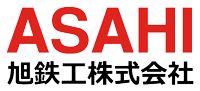
会社名 | 旭鉄工株式会社 |
---|---|
創立 | 1941年(昭和16年) |
本社所在地 | 愛知県碧南市中山町7-26 |
代表取締役社長 | 木村 哲也 |
事業内容 | エンジン、トランスミッション、ブレーキ、サスペンションなどの自動車部品を製造 |
URL | https://www.asahi-tekko.co.jp/ |
関連記事
-
2025.04.25 公開
-松本興産株式会社-
自社開発のアプリで業務効率を大幅に向上 従業員の“デジタル人材化”を後押しする環境づくり松本興産株式会社は、自動車や精密機器などに使われる金属部品の切削加工メーカーです...
-
2024.10.25 公開
-株式会社ミヤックス-
創業75年の老舗がデジタル化で取り組む産官学と協働した地域貢献ビジネス公園の遊具にセンサーやカメラを取り付けて業務のスリム化を模索する実証実験や、デー...
-
2023.08.25 公開
-社会福祉法人みなの福祉会-
人手不足時代の頼れる救世主 ロボット&ICTによる介護の質向上と職員の負担軽減緑豊かな埼玉県秩父郡皆野町で、老人福祉施設を運営する社会福祉法人みなの福祉会は、...
-
-